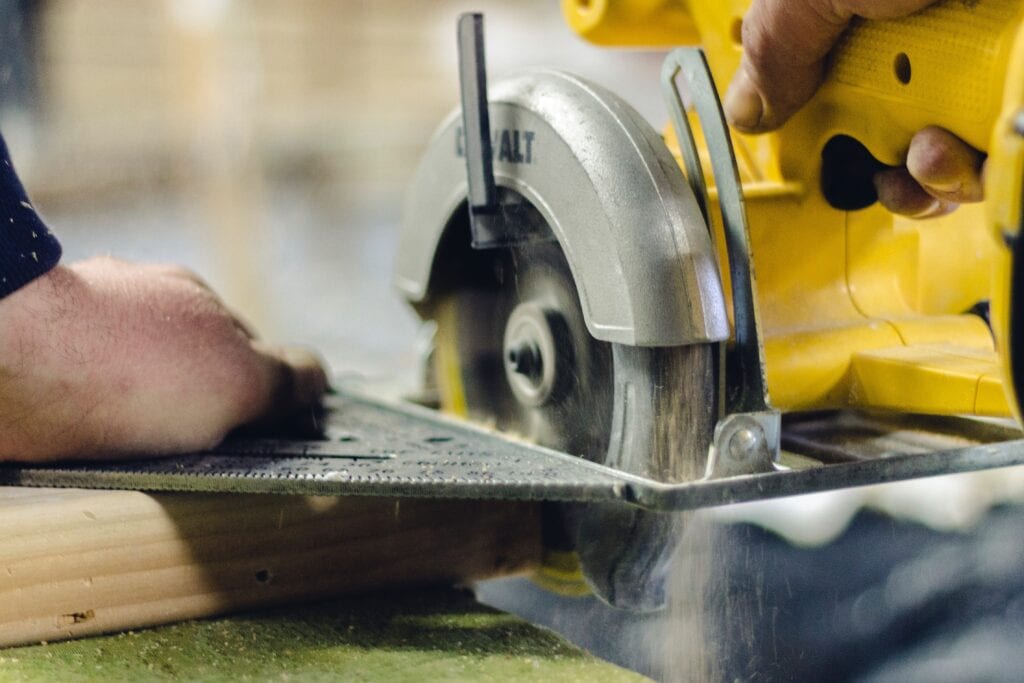
Our workshops are our havens. Creating an obscene amount of sawdust in a short amount of time soothes the soul. Even sweeping the resulting detritus is cathartic. However, we often find ourselves in our zen zone and can quickly disregard the most basic of safety measures which can lead to costly workshop mistakes. Even the most simple of oversights can quickly spell disaster. We’ve put together our Top Ten Workshop Mistakes that every woodworker should avoid in the workshop
1. Removing Safety Features
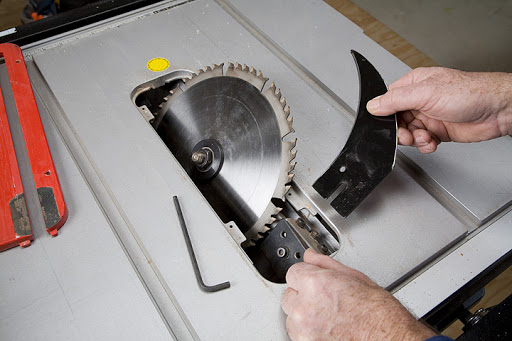
We can make that cut so much quicker if we just remove that blade guard or kickback pawl. Just this once. Once turns into twice and twice turns into always. Before you know it, your safety accessories are collecting dust and a painful workshop mistake is brewing. Make it a habit to keep the included safety features engaged at all times. Disengage these features if you absolutely must but immediately return them to their proper places on all your tools. If a safety feature seems to chronically impede your workflow, you have two choices:
- Adjust your workflow to include the safety features.
- Ditch the tool because it’s poorly designed and incorporate a safer tool which includes better-designed safety elements.
Check out our tool reviews for insight into the safest power tools across all categories.
2. Keeping Tools Plugged In
We concede that some tools can be kept plugged in. After all, an accidental power up of your shop vac shouldn’t cause too much concern for life or limb. However, the risks abound for jointers, table saws, routers, and more in the event that a switch is accidentally engaged or (worse) a child wanders into the shop. Make a habit of always unplugging tools from live power sources. Installing a master cutoff switch to the main power source for your shop is also a fantastic idea if the convenience of keeping everything plugged in can’t be beat.
The annoyance of flipping a switch with no response pales in comparison to the unexpected spooling of a blade at several thousand rpms.
Note that some more modern cordless tools include restart protection safety features. If a battery dies while the tool is turned on, and the switch is kept ‘on’ when a fresh battery is inserted, the tool won’t restart until the switch is toggled off and back on again. An example of this functionality can be found in BOSCH’s GWX18V cordless angle grinder.
3. Drinking in the Shop is an Easily Avoidable Mistake
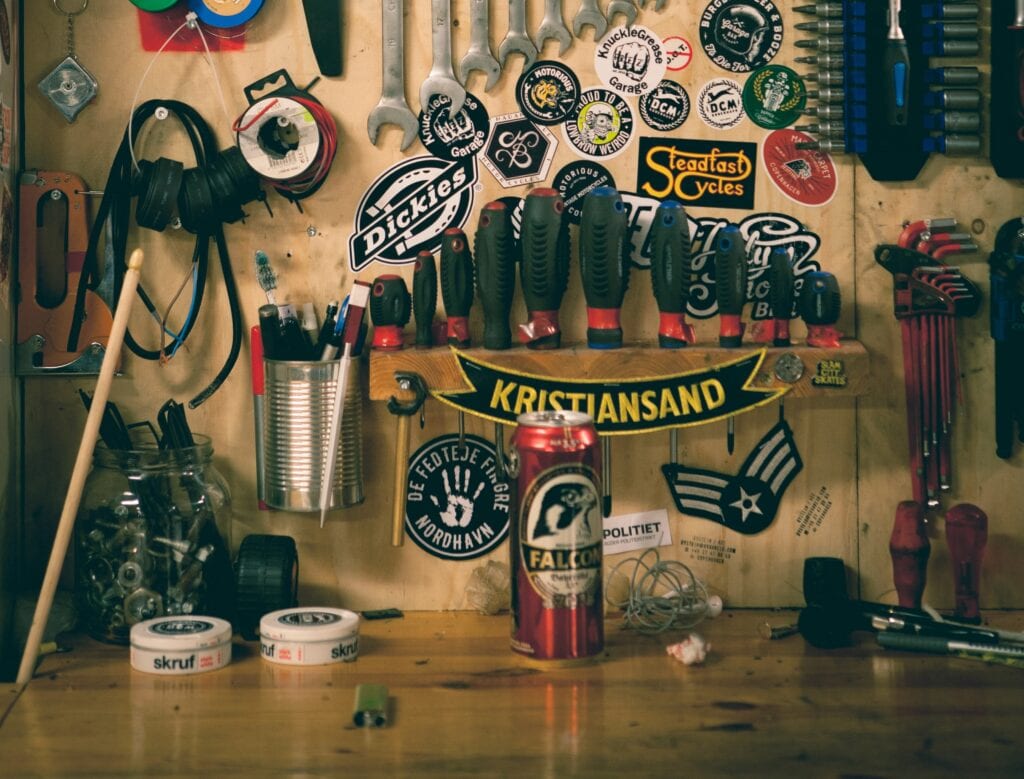
A cold cerveza on a hot day or a whiskey during a brisk evening can’t be beat. Let’s just keep it outside of the shop: deal? Our shops are our sanctuaries and it can be tempting to kick back further with a stiff drink to make the time more enjoyable. We implore you to hold off until the tools are powered down before imbibing. Alcohol can decrease reaction times by up to a tenth of second, which doesn’t seem like much. But the average table saw blade swings 320 teeth in a tenth of a second, which can make or break a devastating workshop mistake. Furthermore, alcohol in the bloodstream reduces the number of platelets. These sticky blood cells cause your blood to clot. Alcohol reduces both the number and ‘stickiness’ of platelets, which can exacerbate a bad situation in the shop.
Can we all agree to hold off until after the blades are quiet? We’ll raise a glass to that.
4. Wearing Loose Sleeves
Those colder shop days make long sleeves a necessity. A loose sleeve, however, can spell disaster if caught up in a jointer or table saw blade. Tight fitting options such as these compression shirts ensure lasting warmth without compromising safety. Baggy sleeves are usually a response to a poorly-warmed shop. If wearing loose-fitting sweatshirts is too much of a temptation, space heaters such as these make cold garages and shops significantly more comfortable.
5. Standing Behind the Saw
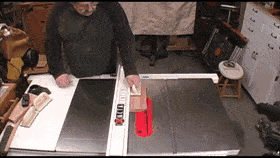
Kickback is real. Although the example above is exaggerated, it highlights the real and present danger that exists directly behind the blade. We at WWC have personally experienced near impalement from rogue offcuts rocketing backwards. Make it a habit to place your body just offset the blade to avoid standing in the line of fire. A well set up pushblock system (like this one from MicroJig) helps alleviate some of the worst workshop mistakes caused by the natural stance behind the saw. Note that this applies to many more tools than just the table saw. Planers, jointers, and router tables all require careful and thoughtful planning when performing cuts.
6. Not Using Push Sticks (WHY??)
One of the best defenses against careless workshop mistakes is a healthy fear (i.e. respect) of power tools. One easy way to practice this respect of power tools is the use of accessories like push sticks. Keeping your hands at a reasonable distance away from spinning blades is fantastic insurance against rapid unplanned digit reorganization, which adversely affects someone in the US approximately every 8 minutes. Push sticks, push blocks, and elaborate combinations are a dime a dozen. Please don’t commit the ultimate workshop mistake by running your fingers unnecessarily close to blades and knives.
7. Free Cross-Cutting
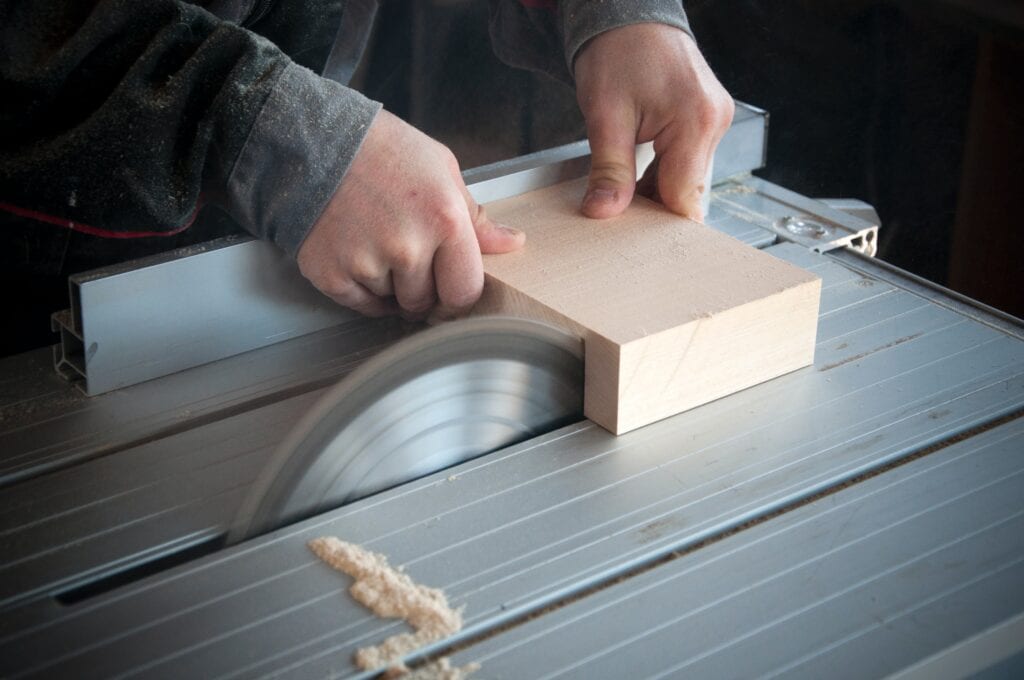
Table saws are great for cross cuts, but these cuts must be adequately supported. The fence is not enough. Miter gauges (our favorite is the Incra MITER27) provide invaluable support for all cross-cutting needs. The issue is that support is required directly opposed to the motion of the blade. The fence provides transverse support, which is not enough. Support directly behind the blade is required and is only available with miter gauges or crosscut fences.
8. Restarting a Cut in the Kerf
We’ve all been there. A cut starts to drift, the fence moves, a kid appears. You have to shut down the saw mid-cut. What do you do? Fire it right back up or start again from the beginning of the cut? As tempting as it is to start the saw spinning while in the middle of the workpiece, this can lead to disastrous results. Minute misalignments between kerf and tooth can quickly cause dangerous kickback scenarios. Take some time and restart the cut from the front of the blade rather than sacrificing safety for a few extra seconds that aren’t really all that precious.
9. Blocked Outfeed Tables are a Common Workshop Mistake
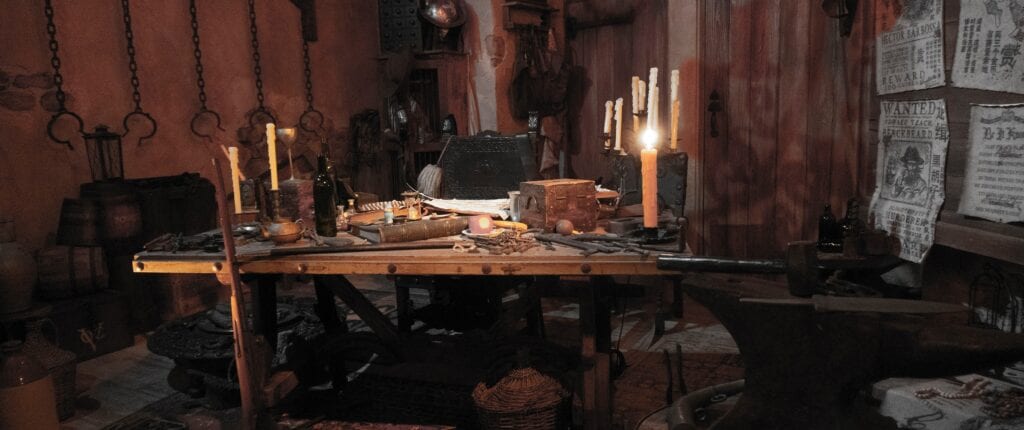
Our projects usually have many parts that find themselves spread amongst all of our surfaces, including our outfeed tables. Keep these clear! There’s nothing worse than ‘almost’ completing a cut only to find you can’t continue because a damn half sheet of plywood is sitting directly behind the blade (see above for midkerf cuts). Before ripping or routing, take a moment to ensure the trailing surface of your tool is free and clear of all tools and debris to avoid a common but avoidable workshop mistake.
10. Not Locking Your Fence
Surely this embarrassment has never happened to you. For the rest of us, do a double check on your fence lock. Anchoring a piece against the fence only for it to wander mid-cut is a recipe for disaster (specifically kickbacks). Make it a habit to always lock the fence after adjustments so that solidly-anchored cuts don’t become unplanned free cuts.